The Lean Construction Playbook
How we maximize value, eliminate waste, and make reliable commitments.
👋 Hey, Kyle here! Welcome to The Influential Project Manager, a weekly newsletter covering the essentials of successful project leadership.
Today’s Overview:
As a project manager navigating traditional construction practices, you may often feel the strain of inefficiencies, waste, and miscommunications – problems that cost time, money, and peace of mind.
To address these issues, "The Lean Construction Playbook" has been created, providing a concise guide filled with Lean Construction principles, strategies, and tools tailored to streamline your project operations and improve value delivery.
This playbook can transform your project management approach, equipping you with knowledge and tactics to minimize waste, enhance team performance, and deliver on commitments more reliably.
This Week’s Newsletter is Brought to You by Disperse.io!
Experience the future of construction with Disperse.io! We’re excited to introduce a groundbreaking construction tech solution that boosts productivity like never before. Disperse is a company I admire because they're committed to removing technological barriers, not creating them.
Meet their latest innovation, "Lookahead." This tool revolutionizes planning by eliminating the tedious tasks of data gathering and manual input.
With Lookahead, your weekly planning becomes a seamless workflow. Simply drag and drop pre-configured task sequences onto the dates and spaces where your subcontractors should be working. This intuitive approach accelerates your planning process by at least 4x and significantly reduces unnecessary communication.
Ready to transform your planning process? Book a call directly at https://www.disperse.io/products/lookahead. Mention that you discovered Lookahead via 'The Influential Project Manager Newsletter’ and enjoy a 10% discount on your first 3 months. Discover how Disperse's Lookahead can make your construction planning effortless and efficient.
The Lean Construction Playbook
Filed under: Lean Tools & Tactics,
Maximizing value, eliminating waste, and making reliable commitments on our projects - aren't these the very things we, as project managers, seek?
Lean Thinking, I've found, holds the keys to achieving these objectives.
These ideas revolve around understanding customer value, streamlining the value chain, and ensuring smooth flow, all while focusing on problem-solving.
But that’s not all. Lean Thinking puts people development and ongoing improvement front and center, with the ultimate aim of reducing waste and enhancing value.
Let's consider our projects: They're essentially a large group of diverse companies, individuals, and skills. When teams are aware of the mindsets, decisions, and processes, they work better.
Smooth processes facilitate efficient information exchange among team members, contributing to project delivery with minimal waste of time, effort, and money.
This Lean Construction Playbook introduces several Lean Thinking principles, processes, and techniques designed to improve your outcomes.
The playbook is segmented into 5 sections:
Mindset & Principles
Defining Customer Value
Efficient Processes & Techniques
Continuous Improvement
Bonus Tools
Whether you're a Lean expert looking to equip your team, or a newcomer starting your Lean journey, this playbook will help you build a more effective work environment.
I'd suggest choosing a few principles and techniques to concentrate on, and begin to experiment with their implementation. Aim for gradual improvement, striving to make your operation 1% better each day.
At the end of the day, Lean Thinking is all about continuous improvement. It's a journey, and every journey starts with a single step forward.
So, let's get started.
Part 1 - Lean Mindsets & Principles
The Lean Construction Institute advocates for six key principles that center around strengthening relationships, promoting shared understanding, and establishing unified objectives. These principles work to breakdown traditional barriers, merging knowledge for the project's overall success, rather than just individual wins.
1. Respect for People
This principle prioritizes the well-being and growth of everyone involved in the project. It matters because a respected and motivated team is more productive. It can be implemented by creating a supportive work environment that values everyone's input and encourages professional growth.
2. Eliminate Waste
This process aims to cut out any steps, materials, or tasks that don't add value to the project. This is relevant as it saves time, resources, and costs. You can achieve this by constantly evaluating and streamlining your processes and removing any unnecessary steps or tasks.
3. Continuous Improvement
This principle revolves around the idea of always looking for ways to do better. It's vital as it keeps your project evolving and improving. Implement this by regularly reviewing your processes and results, learning from your mistakes and successes, and making necessary changes.
4. Value Generation
This principle is about creating the most value for your customer. It's significant because it leads to higher customer satisfaction and repeat business. To implement this, always keep your customer's needs in mind when making decisions, and strive to exceed their expectations.
5. Focus on Flow
This strategy is about ensuring a smooth, uninterrupted workflow on your project. It is crucial for maintaining productivity and meeting deadlines. Implement this by carefully planning and coordinating tasks to avoid bottlenecks and delays.
6. Optimize the Whole
This principle involves looking at the project as a whole, not just individual parts. It's beneficial as it ensures all parts of the project work together efficiently. You can implement this by regularly reviewing the project at a high level to make sure all parts are aligned and working towards the project's overall goal.
Related Article: Delivering The Empire State Building: Lean Construction Principles in Action
Part 2 - Defining Customer Value
For a successful, waste-minimized project delivery, it's essential for your team to pinpoint and document the customer's expectations accurately. The following Lean practices can be handy in capturing the values of the owner and other project team members for a successful outcome:
1. Validation Studies
A Validation Study is a collaborative report that captures the owner’s value proposition as defined by the final business case, budget, schedule, and program of a project.
They keep your projects grounded by checking ideas against reality. To use this, evaluate your project early on for viability and worth, saving time and resources on impossible or low-value tasks. The completed Validation Study acts as a guide for the project team through design and construction process to orient them back to the owner’s value proposition.
2. A3 Thinking
This is a problem-solving approach that fits on a single sheet of A3 (11” x 17”) sized paper. It streamlines thinking and helps you focus only on what's important. Use A3 thinking by identifying problems, analyzing causes, and developing countermeasures on one easily digestible sheet.
3. Choosing By Advantages
This decision-making system focuses on the advantages of each option, rather than their drawbacks. It helps you make the best decision based on positive qualities. Implement it by listing all options, their benefits, and choosing the one with the most advantages.
Unlike systems focused on assessment based on pros and cons, CBA recognizes that cons could also be an advantage for one or more of the other options.
4. Target Value Design (TVD)
Target Value Design (TVD) is a philosophy of designing to a budget instead of budgeting a design. This approach aims to deliver your project within a defined cost limit while meeting quality and functionality needs. It ensures your project doesn't go over budget. Use it by setting a cost limit from the start, and design and make decisions based on staying within that budget.
Part 3 - Efficient Processes
Instead of traditional methods for communication and accountability that tend to harbor wasteful elements, Lean processes equip project teams to balance workloads while reducing waste. Try using some of the following streamlined Lean processes to improve your outcomes:
1. Last Planner System
The Last Planner System (LPS) is made of the five connected conversations to manage activities from early feasibility studies through construction and commissioning. The framework involves five steps:
Master scheduling – Set Key Milestones
Phase scheduling – Specify the Handoffs
Look-ahead scheduling – Make Work Ready
Weekly work planning – Make Promises
Learning – Review variances between planned vs. actual
Projects are started with high-level milestones, then phase pull plans are created as the work proceeds. Look-ahead planning, weekly work planning, and learning (measured through percent plan complete and variances) are implemented to manage the weekly work of the team. This results in reliable and efficient project schedules.
Related Article: Introducing The Last Planner System
2. Pull Planning
Pull planning is a component of the LPS and a process many teams use to start their lean journey.
Pull planning is a powerful way to get designers and trade contractors to make commitments and help schedule the design and construction work. Project team members start with a milestone and then work backward logically to determine all of the steps needed to complete the work and all of the dependencies between the steps.
These processes can break down communication barriers and build collaboration between team members.
Related Article: 13 Proven Strategies for Effective Last Planner Pull Planning
3. The 5S Method
A workplace organization method that follows five steps: Sort, Set in order, Shine, Standardize, and Sustain. It reduces waste and improves efficiency. Implement this by cleaning up, organizing, maintaining order, and repeating these steps regularly. This method can be applied almost anywhere including your: job sites, construction office trailers, whiteboards, calendars, computers, and digital archives.
Related Article: The 5S Lean Methodology
4. Visual Management
This involves displaying important project info visibly so everyone can see it. It promotes transparency and improves communication. Use it by placing charts, schedules, or task cards where everyone can see them.
5. Root Cause Analysis (RCA)
This is a problem-solving method that targets the underlying cause of issues, not just symptoms. It prevents recurring problems. Use it by investigating problems deeply until you find the root cause, then fixing that.
6. Just-in-Time Delivery
This involves ordering materials so they arrive just when you need them. It saves storage space and reduces wasted effort. Use it by carefully scheduling deliveries based on your project timeline.
7. Waste Walks
This is a practice where managers and leaders go to the place where work is being done to observe, ask questions, and learn. It's a powerful way to identify inefficiencies, understand problems, and engage with workers on the front lines.
Implement this by having regular walkthroughs to spot and address the “8 Wastes”:
Over/Under Production
Waiting
Unnecessary Transportation
Over/Under Processing
Excess Inventory
Unnecessary Motion
Defects
Underutilized Talent of Team Members
8. Location Based Scheduling
This is a planning method that ties tasks to specific locations. It improves coordination and reduces conflicts. Use it by linking each task to a specific place in your project schedule.
9. Co-Location
Co-location helps align teams and increases collaboration by having the necessary stakeholders work in the same office. While larger projects can co-locate for extended periods on a project, smaller projects can co-locate for shorter sessions for increased efficiency.
For example, this can be done for one day every two weeks or by using online tools.
10. Building Information Modeling (BIM)
BIM is used during design and construction for coordination, prefabrication, scheduling, cost estimating, and facilities management. This is a digital representation of physical and functional characteristics of a facility. It enhances coordination and reduces mistakes. Use it by creating and using a digital model of your project.
11. Information Management
This is the collection, storage, and distribution of project information. It ensures everyone has the info they need. Implement it by creating and following a clear process for managing project information.
12. Project Dashboards
These are visual tools for tracking project progress. They provide an at-a-glance view of project status. Use it by setting up a dashboard that tracks key project metrics. Essentially, they serve as a central hub for project information, promoting transparency and efficiency.
13. Offsite Construction / Prefabrication
This involves assembling parts of the project at a different location before installing them on-site. It utilizes skilled shop labor, leading to higher quality and productivity. Prefabrication also enhances safety, reduces risk, and provides more predictable project costs by eliminating unnecessary steps. Use it by planning for offsite fabrication where possible. For maximum effectiveness, it's recommended to start this process early in the project lifecycle.
For more information: See the website of Lean Construction Institute.
Part 4 – Continuous Improvement
High-performing teams keep a laser focus on continuous improvement throughout a project's lifecycle. It's crucial for teams to stay mindful of their processes, ready to reflect and refine them at the first hint of a hitch. Use the following lean tools to encourage and commit to continuous improvement:
1. Percent Plan Complete (PPC)
Another component of the Last Planner System, Percent Plan Complete (PPC) is a lean construction tool used to measure the reliability of project planning. It's calculated by dividing the number of tasks completed by the number of tasks that were planned to be completed, then multiplying by 100 to get a percentage. This metric provides a clear picture of how well the project is adhering to its schedule. To use PPC, regularly compare your planned work with what's actually been completed and take action where needed.
2. Plan / Do / Check / Adjust (PDCA)
PDCA is a repetitive four-step management method used for the control and continuous improvement of processes. It's useful for implementing change and solving problems. Apply PDCA by planning a change, carrying it out, checking the results, and adjusting your approach based on those results.
3. Plus / Delta Thinking
This is a review technique where you identify what went well (Plus) and what could change for the better (Delta). It encourages continuous improvement. Implement it by holding regular team discussions where you ask these two questions about your recent work.
4. Ask Why 5x
This is a problem-solving technique that digs into the root cause of a problem by asking "Why?" five times. It prevents issues from recurring by addressing their source. Use the 5 Whys when you face a problem: start with the issue and ask "Why?" until you reach the root cause. Once the team discovers the root cause, it should find solutions to remove the root cause, helping to resolve similar issues in the future.
Part 5 - Bonus Tools Project Management
Staffing Plans: These are essential tools for ensuring that you have the right people in the right roles at the right time. They help in managing resources effectively and avoiding over or under-staffing.
Roles & Responsibility Matrix: This tool clearly defines who is responsible for what in the project. It eliminates confusion and ensures accountability, leading to smoother project execution.
Budgeting Metrics: These provide a clear picture of the project's financial health. They help in tracking costs, managing budgets, and making informed financial decisions.
Scheduling Metrics: These are crucial for tracking project progress and ensuring timely completion. They help in identifying delays early and taking corrective action.
Risk Registers: These are tools for identifying, assessing, and managing potential risks. They help in proactive risk management and mitigation, reducing project uncertainties.
RAID Logs (Risks, Assumptions, Issues, & Decisions): These are comprehensive tools for tracking and managing various aspects of the project. They help in maintaining transparency and ensuring that nothing falls through the cracks.
Final Takeaways:
Using these principles and tools, project managers can strive to finish projects on time, within budget, and to the quality expected by their clients.
Most people who've learned about lean construction can see its advantages. But shifting to this new way of doing things means changing how we work, and that's not always easy. Companies have to tackle the challenge of changing habits that are deeply ingrained.
In my view, Lean Construction is more than just a method - it's a way of thinking. To reap the benefits, you have to apply this mindset to all your projects. It's not a quick fix - it calls for leadership, focus, discipline, and a real drive to get things done.
Until next week,
Kyle Nitchen
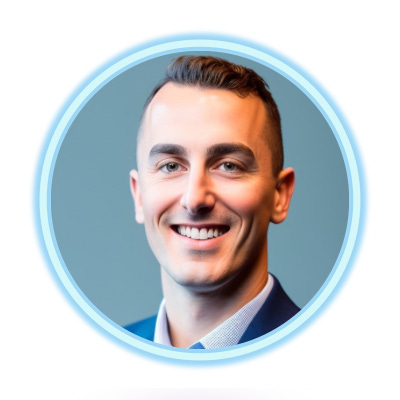
Before you go, here’s how I can help:
Upgrade your PM software. Project financials, management, and construction admin. Switch to INGENIOUS.BUILD to evolve from an administrative project manager to strategic project leader.
Get my full toolbox (free). It contains 30+ software and hardware tools I’m using today.
Hold your schedule accountable. Gain stability and flow in your projects with this Takt Planning & Control online course. Use code “Influentialpmtakt” for 30% off!
Advertise in this newsletter. Put your brand in front of 2,500+ construction project managers, leaders, and execs. (Booked out 5 weeks)
Support this Newsletter. The Influential Project Manager articles will remain free, but if you find this work valuable, I encourage you to become a paid subscriber. As a paid subscriber, you’ll help support this work.