Introducing The Last Planner System
The ultimate project production management tool to reduce waste and remove constraints.
👋 Hey, Kyle here! Welcome to The Influential Project Manager, a weekly newsletter covering the essentials of successful project leadership.
Today’s Overview:
Boost your project management and production game with the Last Planner System.
Learn how to implement the five key elements of the LPS framework: Master Planning, Phase Pull Planning, Look-Ahead Planning, Weekly Work Planning, and Daily Huddles/Learning.
Discover the benefits of adopting the LPS approach, including increased collaboration, transparency, productivity, and overall project success.
Today’s Newsletter is Brought to You by Taliho.
Taliho is a document storage platform with a revolutionary twist perfectly tailored for the construction industry. Their patented technology enables users to construct customized arrangements of QR Codes.
Each unique code within the QR Arrangement is pre-programmed to provide remote access to a specific "Category" of construction project data. Post your QR Arrangement in the field, where remote users with mobile devices simply scan and instantly retrieve the information they are seeking - without having to burden the PM, or stop work waiting for it.
Select from our Categories, or create your own. Taliho was built to be simple, intuitive and flexible.
Sign Up for a 14-Day Free Trial at www.taliho.com.
Introducing The Last Planner System
Filed under: Lean Tools & Tactics
Lean thinking is one of the pillar values when it comes to Influential Project Management.
Lean thinking is a term used to describe the process of making business decisions in a Lean way.
Today we’re covering a lean construction tool that helps you plan, execute, and improve your projects. You don't want to miss out on this valuable resource for successful project management!
The built environment is complex, and project managers are always looking for ways to streamline their work and gain more reliability in their operation. The Last Planner System (LPS) is one such tool that has become increasingly popular in recent years.
This framework, when implemented right, will make project execution your unfair advantage.
What is Lean Construction?
Did you know? Among contractors using lean methodology, 84% experience higher quality, 80% see greater customer satisfaction, 77% enjoy increased productivity, and 77% note improved safety.
Yet, surprisingly, 90% of people are not fully informed about these effective strategies.
Lean construction is certainly an industry buzzword, and many companies see the value in its implementation; however, it is not universally used, likely due to a lack of knowledge on the topic or proper tools for implementation.
Lean construction is a project delivery process that aims to maximize stakeholder value while minimizing costs, time, effort, and materials used for the entire project.
It is a collaborative approach that involves all stakeholders in the construction process, from owners to contractors, to ensure project success.
The Last Planner System focuses on these lean construction principles by introducing planning and management framework to improve predictability and productivity on construction projects.
What is the Last Planner System?
The Last Planner System is a project management and production tool that is designed to improve collaboration and communication among construction teams. It promotes the creation of predictable workflow among various parties so that the group achieves reliable results. The system allows potential hurdles to be found and addressed before they slow down the flow.
The Last Planner System focuses on three main aspects of construction project management: planning, execution, and review.
In traditional design and construction projects, the level of follow-through on commitments made is unfortunately low. On average, only 54% of work planned for a given week is completed within the allotted schedule. As a result, the vast majority of projects are delivered late and over-budget, stakeholders end up not being satisfied with the end result, and workers suffer injuries on the job. - Lean Construction Institute
By implementing the Last Planner System, project managers can:
Improve communication
Increase efficiency
Enhance predictability
How did the Last Planner System get its name?
The Last Planner System (LPS) is a project management framework created by the Lean Construction Institute in the 1990s.
The name "Last Planner System" refers to the last person who plans the work on a construction project, typically the foreman or superintendent.
The idea behind this is that the people who are closest to the work are the best equipped to plan it.
The Last Planner System empowers these individuals to take ownership of the planning process and ensures that all team members are involved in the planning and execution of the project.
How It Works: The 5 Connected Conversations
LPS has become one of the most popular frameworks used for production in the design and construction industry. Why?
Because it does a great job of connecting the many conversations that happen at different levels across time. The majority of the unsatisfaction and issues that happen on a project is a result of conversations that were never had or had with the wrong person at the wrong time.
From the project executive all the way down to the trade specific foreman - LPS is a collaborative planning process that involves all members of the project team.
The Five Connected Conversations include:
Milestone Planning - Set Key Milestones
Phase Pull Planning - Specify the Handoffs
Look Ahead Planning - Make Work Ready
Weekly Work Planning - Make Promises
Learning - Review variances between planned vs. actual.
Let’s go through each.
You’ll notice as you move down the production funnel, the conversation elements change with time.
We should → We should/can → We can —> We will —> We did.
It’s important to be aware of where you’re at in the production conversation so you can be most effective.
Milestone Planning (30,000 Ft.)
The project team creates a master schedule that outlines the overall timeline of the project as well as the major milestones that the timeline is based on.
This is often the P6 master schedule that ends up becoming the contract schedule between the owner and construction manager.
In this stage, set milestones and strategy of what you SHOULD do, while identifying long lead items.
Phase Pull Planning (10,000 Ft.)
The team then breaks the project down into smaller phases and creates a schedule for each phase.
In this stage, specify the hand offs, identify any operational conflicts, to start to identify what you CAN do from what you SHOULD do.
Look Ahead Planning (1,000 Ft.)
The team then creates a look-ahead schedule for the upcoming week or two, which outlines the specific tasks that need to be completed during that time.
In this stage, we look-ahead to assure that the future work is made ready, so it CAN be done.
Weekly Work Planning (100 Ft.)
The team then meets to create a weekly work plan, which outlines the specific tasks that need to be completed during the upcoming week.
In this stage, we make reliable commitments (promises) for the work that you WILL do.
Daily Huddles (10 Ft.)
The team holds a daily huddle to discuss progress, identify any obstacles or issues, and make any necessary adjustments to the plan.
Learning (0 Ft.)
Before the next weekly work plan, the team meets to review the “percent of promises complete” (PPC) in effort to continuously improve.
What promised work from last week didn’t get complete and why?
In this stage, we dive deep into reasons for failure, and develop/implement lessons learned.
The Last Planner System, when executed right, enhances all of 6 principles of lean construction:
Respect is increased when team members collaborate to solve problems
Waste is removed when work is done correctly the first time
Flow is enhanced through careful planning
Value increases as more time and resources are allocated towards value-adding procedures
Continuous improvement occurs when the team learns from each breakdown in a cycle of planning, and the whole is optimized with better outcomes.
Visualizing The Levels of Granularity
I find it helpful to visualize the different levels of granularity this framework covers.
Starting with boulders, these represent the most significant aspects of the project, such as the project's biggest milestones or goals.
The next level of granularity, represented by rocks, consists of the specific strategies or plans required to achieve the project's objectives.
Pebbles, represent the more detailed tasks required to execute the project's strategies. These tasks could include specific deliverables or mini milestones that need to be achieved.
Finally, sand represents the most granular level of the project, day-to-day, consisting of the specific actions that individuals take to complete smaller tasks.
By visualizing the levels of granularity in this way, project managers can better understand the project's different levels and their inter-dependencies. They can prioritize the most critical aspects of the project while also ensuring that all necessary tasks are completed.
Implementing The Last Planner System
Adopting the Last Planner System requires a cultural shift in the way that construction projects are managed.
Project managers and superintendents must be willing to embrace a collaborative approach to planning and execution and empower their team members to take ownership of the process.
To apply the Last Planner System, project management teams should expect to:
Educate team members on the Last Planner System and the benefits of collaborative planning.
Involve all team members in the planning process, including subcontractors and suppliers.
Encourage open communication among team members and foster a culture of trust and collaboration.
Implement a system for tracking progress and making adjustments to the plan as necessary.
Provide training and support for team members to ensure that they are comfortable using the Last Planner System.
In conclusion, by adopting this new framework, project management teams can improve collaboration and communication among team members, reduce delays, and ensure that projects are completed on time, within budget, and to the desired quality standards.
Let’s make project execution your unfair career advantage!
What new actions or ideas that you learned today can you take back to your project?
Let me know in the comments or send me a message.
Until next week,
Kyle Nitchen
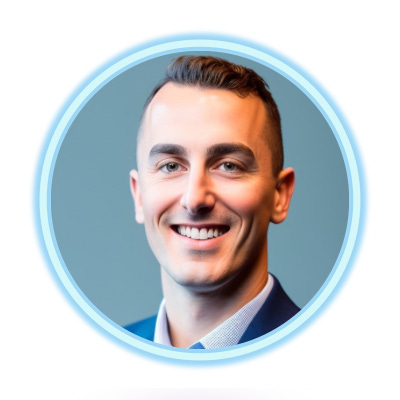
When you're ready, here’s how I can help:
Upgrade your PM software. Project financials, management, and construction admin. Switch to INGENIOUS.BUILD to evolve from an administrative project manager to strategic project leader.
Get my full toolbox (free). It contains 30+ software and hardware tools I’m using today.
Hold your schedule accountable. Gain stability and flow in your projects with this Takt Planning & Control online course. Use code “Influentialpmtakt” for 30% off!
Advertise in this newsletter. Put your brand in front of 2,500+ construction project managers, leaders, and execs. (Booked out 5 weeks)
Support this Newsletter. The Influential Project Manager articles will remain free, but if you find this work valuable, I encourage you to become a paid subscriber. As a paid subscriber, you’ll help support this work.