👋 Hey, Kyle here! Welcome to The Influential Project Manager, a weekly newsletter covering the essentials of successful project leadership.
Today’s Overview:
The Empire State Building has captivated the hearts and minds of millions since it first pierced the New York City skyline, symbolizing the spirit of human ambition and creativity.
Today we’re exploring the Empire State Building's extraordinary delivery using lean construction principles before they were formally recognized. It includes a in-depth examination of key patterns, techniques, and project management strategies that led to the iconic building's success.
As you'll discover, the making of this marvel provides numerous valuable insights to apply in your own construction projects, enhancing efficiency, communication, and overall project results.
🏗 The Empire State Building Unveiled:
The Timeless Lean Construction Strategies Behind One of History's Greatest Projects.
Filed under: Construction, Lean Tools & Tactics
Project Team:
Owner: Empire State, Inc.
Architect: Shreve, Lamb, & Harmon Associates
Contractor: Starrett Brothers and Eken
New York's Empire State Building was one of the most successful projects of all time.
The vision that became arguably the world’s most legendary skyscraper started with a pencil. The architect, William Lamb took a pencil from a desk and held it up vertically, point up.
That’s what the Empire State Building would be: slim, straight, and stretching higher into the sky than any other building on the planet.
The primary duo behind the construction of the Empire State Building was John J. Raskob and Al Smith.
Raskob, a self-made business mogul and onetime chairman of the General Motors Corporation finance committee, together with Smith, who was a former Democratic governor of New York.
They settled on a location - the site of the original Waldorf-Astoria hotel - set the parameters of the project, and developed the business plan. They fixed the total budget, including the purchase and demolition of the Waldorf-Astoria, at $50 million ($820 million in 2022 dollars), and scheduled the grand opening for May 1, 1931. They hired Lamb’s firm. At this point, they had 20 months to go from first sketch to last rivet.
In planning the building, Lamb’s focus was intensely practical. Working closely with the project’s builders and engineers, Lamb developed designs shaped by the site and the need to stay on budget and schedule.
“The designs were rigorously tested to ensure that they would work. Hardly a detail was issued without having been thoroughly analyzed by the builders and their experts and adjusted and changed to meet every foreseen delay.” - William Lamb
The site broke ground on March 17, 1930. More than 3,000 workers swarmed the site, and construction advanced rapidly, beginning with the steel skeleton, thrusting upward, followed by the completed first story. Then the second story. The third. The fourth.
As workers learned and processes smoothed, progress accelerated. Up went three stories in one week. Four. Four and a half. At the height of construction, the pace hit a story a day. And a little more.
“When we were in full swing going up the main tower, things clicked with such precision that once we erected fourteen and half floors in ten working days - steel, concrete, stone, and all.”
By the time the Empire State Building was officially opened by President Hoover - exactly as scheduled, on May 1, 1931 - it was already a local and national celebrity. Its height was daunting. The efficiency of its construction was legendary.
Even though practicality had been at the front of Lamb’s mind, the building was unmistakably beautiful. Lamb’s drive for efficiency had created a lean, elegant design, and the American Institute of Architects (“AIA”) awarded it the 1931 Medal of Honor. Then, in 1933, King Kong climbed the building on the movie screen, and the Empire State Building became a global star.
The Empire State Building had been estimated to cost $50 million. It actually cost $41 million ($679 million in 2021). That’s 17% under budget. Construction finished several weeks before the opening ceremony.
To this day it remains an astonishing feat of planning, design, engineering, & construction.
A few critical patterns and principles contributed to the exceptional success of the Empire State Building. Remarkably, many of these principles resemble lean construction concepts, even though they were implemented 25 years before the formalization of lean construction.
This impressive achievement prompts us to consider the following questions:
How did a project as complex as the Empire State Building achieve such remarkable success?
What principles, strategies, and tactics contributed to its success?
How can we replicate this success on every project?
Lean Construction Principles in Action
Within just 20 months, the building was planned, engineered, granted permits, had the existing structure torn down, and the new building was constructed. On time and under budget.
In the following sections, we'll explore the lean methodologies and strategies employed during the construction of the Empire State Building.
1. Clear Objectives & Strong Client Direction
From the very beginning, it's crucial to note that the Empire State Building project was defined by clarity and strong direction.
Clear objectives are vital for predicting outcomes, and projects with crystal-clear goals and priorities often yield greater success. Smooth and effective decision-making and day-to-day communication are made possible when everyone keeps the mission at the forefront of their minds. Accountability becomes more manageable when everyone understands the mission fully.
The Empire State Building serves as an excellent example of this principle in action. The client had one goal and the project team understood it, clear as day.
Speed was the driving force from day one. The project had well-defined goals, including an ambitious 410-day construction schedule and a fixed budget. The Empire State Building's stakeholders were united by the sole objective of constructing the world's tallest building, completed and ready for tenants by May 1, 1931.
This clarity facilitated efficient decision-making and resource allocation throughout the entire process.
2. Optimizing the Whole
The Empire State Building construction prioritized the overall success of the project, rather than focusing on individual components.
Empire State, Inc. was quick to realize the importance of collaboration. They knew that the design of the project could not be planned by the architects alone.
They assembled an expert team including the owners, contractors, architects, structural and mechanical engineers, elevator consultants, and rental agents that were required to collaborate. If the someone in the group had a problem, they were challenged first to define the problem and then to solve it.
This approach of collaborative production and decision making by involving key stakeholders other than the designer from the early stage of the project is a classic integrated project delivery / lean delivery system.
3. Collaborative Decision Making
Empire State, Inc. set up a building committee to make timely decisions in order not to impede progress on the plans and construction.
These regular meetings between architects, engineers, and contractors allowed for open communication, leading to the resolution of potential conflicts, and efficient decision-making.
Shreve, Lamb and Harmon made innovative design decisions in consultation with the committee to speed construction. Starrett Bros. & Eken continued to look for more efficiency by improving the system.
They were able to realize that in order to achieve their goal they had to focus on the overall system.
This simple understanding forms the underlying principle of lean construction. The collaborative team approach, united under the common goal.
4. Target Value Design
The Empire State Building's success can be partially attributed to the effective use of Target Value Design (“TVD”) during its planning and construction process. TVD is a management practice that focuses on designing a project to meet specific performance, schedule, and cost objectives. In the case of the Empire State Building, the design and construction were guided by clear financial and functional targets, which enabled the project team to make informed decisions at every stage.
This approach allowed the project team to prioritize cost-saving innovations, such as the use of prefabricated steel components. This innovative construction technique allowed the owner to save both time and money, as the components could be manufactured offsite and quickly assembled on location. This not only expedited the construction process but also ensured that the project stayed within budget.
The TVD approach ensured that all aspects of the project were carefully considered and aligned from the outset. As a result, the team was able to make strategic decisions that optimized resources, reduced waste, and maximized value for the client.
5. Fast Tracking
Time had to be scheduled nearly to the minute. The schedule dictated that each section of the building process overlapped - not a moment was to be wasted.
The Empire State Building was the first commercial construction project to employ the technique of fast-track construction, a commonplace approach today but very new in the early 20th Century. This technique consists of starting the construction process before the designs are fully completed in order to reduce delays and inflation costs.
The demolition of the Waldorf-Astoria began just two days after the general contractor was brought on board, before even the preliminary designs had been completed. Construction on the foundations would similarly start before demolition was completed.
When steel erection commenced in April of 1930, the upper floors were still being designed - over the course of the project, each level of structural steel was designed just a month ahead of when the order was due at the mill.
6. One Touch Material Handling
The construction of the Empire State Building was a pioneering example of efficient "One Touch Material Handling," which contributed to the project's remarkable speed and success. This approach to material management minimized the handling and movement of materials, thus reducing the time, labor, and resources required for the construction process.
Trucks drove directly into the belly of the building, allowing the materials they carried to be seamlessly transferred from the truck beds to the construction site. This eliminated the need for intermediate storage or additional handling, as the materials were hoisted directly to the floors where they were needed.
This streamlined process was supported by a meticulously planned inventory management system. Inventories were carefully calculated to accommodate no more than three days' worth of material at a time, ensuring a constant and efficient flow of supplies without excessive storage or waste.
The "just-in-time" flow of materials to the site was so efficient that rumors circulated about steel beams arriving from the steel forging plants to the building too hot to touch with bare hands.
This anecdote says something about the speed and coordination achieved during the construction process, which contributed to completing the Empire State Building ahead of schedule.
7. Solid Supply Chain
The companies and suppliers they hired had to be dependable, able to provide quality work, and willing to adhere to the allotted timetable.
To achieve this, the contractor rigorously monitored the supply chain by pre-qualifying suppliers, manufacturers, and subcontractors, assessing their ability, facilities, manpower, and capacity to take on a project of such magnitude. This thorough evaluation ensured that every party involved was well-suited to contribute to the construction's success.
For example, the steel erection was let to Post & McCord, who attacked its problem on its own initiative and worked out a plant layout and performance schedule which highly satisfied the contractor.
Furthermore, Starrett Brothers & Eken, the project's lead contractors, employed expediters both prior to and during the construction of the Empire State Building. These expediters were responsible for assessing production capacities at quarries in Italy, Belgium, and Germany, as well as examining railroad facilities, ports, and connections with Atlantic shipping to ensure seamless material transportation.
8. Focus on Flow
The Empire State Building project focused on flow and work structuring, effectively organizing tasks into manageable segments that produced a predictable workflow.
The pace of the entire schedule was controlled by four major structural operations: erection of steel, construction of floor arches, exterior metal trim, and exterior limestone. By organizing the work chunks in this way, unnecessary traffic could be limited and more work could be completed.
The intention was to control the production of more than 60 major trades grouped into four streams, each led by a pacemaker. In lean assembly, establishing work flow predictability is crucial - a set amount of time for specific activities helps to regulate production levels more than any other technique.
The pacemaker approach adopted in the Empire State Building project allowed Starrett Brothers & Eken to know exactly how far ahead or behind they were on any particular task.
While the outside of the building was being constructed, electricians and plumbers began installing the internal necessities of the building. The timing for each trade to start working was finely tuned. As Richmond Shreve described:
When we were in full swing going up the main tower, things clicked with such precision that once we erected fourteen and a half floors in ten working days - steel, concrete, stone and all. We always thought of it as a parade in which each marcher kept pace and the parade marched out of the top of the building, still in perfect step. Sometimes we thought of it as a great assembly line - only the assembly line did the moving; the finished product stayed in place.
As a result, every trade completed their work faster than required by the schedule:
9. The 5S Methodology
Throughout the design and construction of the Empire State Building, the 5S Lean Methodology played a significant role in optimizing the workspace and material handling system for maximum productivity.
The job site was strategically organized, so that materials were readily accessible to workers with minimal effort. This streamlined approach reduced downtime and increased efficiency.
In addition to efficient material placement, a dedicated crew was assigned to maintain site housekeeping. This team focused on promptly removing waste materials and preventing clutter from accumulating in work areas.
10. Offsite Fabrication
The Empire State Building utilized offsite fabrication to streamline the construction process and reduce the amount of on-site preparation work. This approach required materials to be produced in as close to a finished state as possible before arriving at the site.
A prime example is the 60,000 tons of steel framework, manufactured in Pittsburgh and swiftly transported to New York via train, barge, and truck. The steel posts and beams arrived at the site with designated markings, indicating their position in the framework and the number of the derrick assigned to hoist them.
This efficient system enabled workers to quickly swing the girders into place and secure them with rivets. In some cases, the steel components were installed just 80 hours after leaving the furnace and rolling off the production line.
Offsite fabrication was crucial in accelerating the construction timeline and contributing to the project’s unprecedented success.
11. Lean Thinking: Minimize Waste + Maximize Value
Lean thinking focuses on the elimination of non-value added activities.
The Empire State Building project exemplified legendary efficiency, with contractors implementing numerous lean innovations that conserved time, resources, and manpower.
A variety of strategies and techniques were employed during the Empire State Building's construction to reduce waste and maximize value at every stage. These innovative and highly efficient methods ensured materials were delivered exactly when and where they were needed.
Some noteworthy examples include:
When material arrived on site, it was either lifted upward by a hoist or derrick or put in a rail car and sent to the appropriate floor.
Concrete batch plants were built in the basement to avoid having to truck in concrete.
Special brick hoppers were built that allowed bricks to be dumped from the truck and raised to the proper floor without a human hand ever needing to touch them.
To minimize the time workers spent traveling to get food, cafeterias (set up by a local restaurant) were set up on the third, ninth, twenty-fourth, forty-seventh, and sixty-fourth floors.
But the most notable was the narrow-gauge rail track (called the “industrial railroad”) that was installed on each floor, which allowed material to easily be moved to the appropriate location by way of mine carts.
Final Takeaways:
As you can see, The Empire State Building stands as a shining example of Lean Construction principles in action, even before these concepts were formalized.
This project provides invaluable lessons for today's construction professionals aiming to optimize their work.
In closing, I encourage you to contemplate these lean concepts and determine which ones can be incorporated into your projects. Key takeaways include:
Clear objectives and strong client direction: Establish explicit goals and maintain open communication between stakeholders to drive project success.
Optimizing the whole: Prioritize the overall project's success over individual aspects to achieve cohesive and efficient results.
Collaborative decision making: Foster teamwork and encourage shared input to create informed, well-rounded decisions.
Target Value Design: Balance functionality and budget constraints by designing with clear financial and performance targets in mind.
Fast Tracking: Accelerate project timelines by overlapping tasks, reducing downtime, and enabling concurrent progress.
One Touch Material Handling: Streamline logistics by minimizing material handling and storage for increased efficiency.
Solid Supply Chain: Ensure reliable suppliers, manufacturers, and subcontractors by conducting thorough pre-qualification assessments.
Focus on Flow: Optimize work processes to maintain a continuous, predictable workflow and prevent bottlenecks.
The 5S Method: Create a clean, organized, and efficient workspace by implementing the 5S principles (Sort, Set in order, Shine, Standardize, Sustain).
Offsite Fabrication: Reduce on-site labor and accelerate construction timelines by utilizing pre-assembled, ready-to-install components.
Lean Thinking: Minimize waste and maximize value through continuous improvement, eliminating non-value-added activities, and optimizing resource utilization.
By adopting these principles, project leaders can effectively manage costs, enhance efficiency, and deliver outstanding results, mirroring the groundbreaking success of the Empire State Building.
Until next week,
Kyle Nitchen
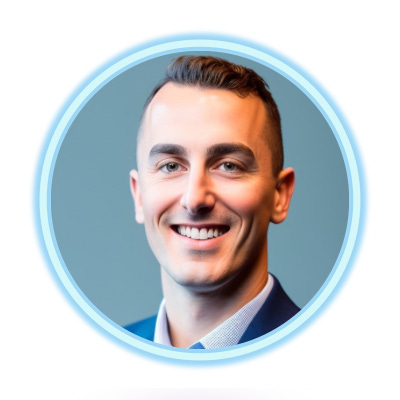
Whenever you're ready, there are 5 ways I can help you:
Get my first book! No Bullsh*t Project: A Project Manager’s Guide to Successful Project Leadership
Upgrade your PM software. Experience the future operating system for construction and real estate development.
Get my full toolbox (free). Access 30+ software and hardware tools I'm using today.
Learn Takt Planning. Elevate your skills as a scheduler, planner, and lean builder with the Takt Planning & Control online course. Use code "Influentialpmtakt" for 30% off.
Advertise in my newsletter. Put your brand in front of 5,300+ construction project managers, leaders, and execs. (Booked out 5 weeks)
Great article!!
Excellent write up!