10X the Impact of Your Procurement
Strategies to help you successfully manage the construction supply chains.
👋 Hey, Kyle here! Welcome to The Influential Project Manager, a weekly newsletter covering the essentials of successful project leadership.
Today’s Overview:
Construction supply chains are sometimes long and complex, making them seem impossible to manage.
Procurement issues cause almost 50% of project schedule delays. Yet, at best, project teams use outdated thinking and ad-hoc spreadsheets to plan and track procurement!
Getting the right material in the right quantity to the right place at the right time is critical for achieving construction cost, schedule, and use-of-cash objectives. The following recommendations lay out a workable, practical plan.
Today’s newsletter is proudly presented by ConstructivIQ!
Did you know procurement issues cause nearly 50% of project schedule delays? It's time to ditch the spreadsheets and embrace a smarter approach with ConstructivIQ. Plan, track, and manage all procurement activities in lockstep with your construction project schedule.
Craft a robust procurement strategy.
Sync Procurement With Your Project Timeline.
Track and Drive Procurement Priorities.
Navigate Changes Effortlessly.
Seamlessly Integrate With Your Favorite Tools.
Learn and Optimize Future Projects.
Tackle your procurement process and conquer challenges head-on with ConstructivIQ. Ready to change the game? Try our software for free and get ready to crush it.
🕒 10X the Impact of Your Procurement
Filed under: Project Management, Construction
Have you ever tried building something without the right material?
It’s a mess. Or just plain impossible.
And yet, it happens in construction all time.
Well, as an Influential Project Manager, it’s your job to get the right materials to the job when you need them. This critical process is known as procurement.
Procurement is simply the act of buying or acquiring what you need.
If we procure our materials too early, we deal with excess inventory, potential damages, and the risk of becoming them becoming outdated due changes.
If we procure our materials too late, we impact the flow of production and scheduled milestones.
In other words, without the right materials at the right time, we’re stuck.
Procurement issues cause almost 50% of project schedule delays. Yet, at best, project teams use outdated thinking and ad-hoc spreadsheets to plan and track procurement!
Today, we're addressing why procurement can be a real pain and how to turn it into your project's life force.
What’s the Current State of Procurement in Construction?
When it comes to managing materials for a construction project, there’s a common saying:
“It’s better to have it and not need it, than to need it and not have it.”
This mindset leads to materials being ordered and stored on-site long before they're needed. Why does this happen?
Suppliers and contractors make their money from selling and handling these materials.
Planners use these expenses as “progress” based on earned value analysis.
Owners feel reassured seeing materials on-site, interpreting it as “progress.”
This creates a cycle where spending money is seen as making progress. If 20% of the budget is spent, the project is perceived as being 20% complete, regardless of the actual progress. This approach satisfies everyone on the surface – the owner, the manager, and the supplier all see what they want to see.
The drive to boost worker productivity has led to a rush in getting materials on-site as quickly as possible. However, this rush for productivity can actually slow us down, confusing being “busy” with making real progress.
Read also: Why is it So Hard (and Expensive) to Build Anything?
Many in the industry accept the costs of storing, securing, and risking materials becoming outdated as just part of doing business. 90% of construction professionals believe that having materials waiting for workers is preferable to having workers wait for materials.
But this thinking is flawed. It leads to wasted resources, time, and money, and increases the risk unnecessarily. It’s a classic case of good intentions leading to bad outcomes.
The solution? Shift from a "just in case" to a "just in time" mindset. You can achieve this by creating an “intelligent” procurement plan.
Let’s breakdown how you can do exactly that.
How to Build an “Intelligent” Procurement Plan
The current strategy of “get everything out as fast as possible” has time-related, financial, and productive cost.
The right material in the right quantity at the right place and the right time is critical for achieving objectives related to construction cost, schedule, and use of cash objectives.
With that said, what, specifically, can we do about the problem? The following strategies lay out a workable, practical plan.
#1 Synchronize your supply and demand.
Synchronizing your supply (material) with your demand (master schedule) is the first key principle to get right. Different materials have different workflows so it’s important you map out the process for each one.
Once you achieve this synchronization, you’ll be able to organize all procurement activities/durations according to the forecasted dates and pinpoint dependencies.
This level of coordination is the key to materials arriving just when needed – eliminating the risk of premature delivery or delays.
#2 Create a REAL procurement plan.
Construction projects have a detailed master schedule. But procurement planning is done in an ad-hoc, siloed manner using spreadsheets at best.
Ditch the manual spreadsheets. Create a comprehensive plan in collaboration with all your stakeholders that includes all relevant procurement activities and is linked to the master schedule.
Your plan should include the design, engineering, buyout, submittals, ordering, manufacturing, delivering, and their dependencies to give visibility to everyone involved.
With everyone on the same page, procurement becomes a shared mission, not a siloed task.
#3 Embrace supply chain management (not just procurement).
Unlike the accepted practice that is focused on buying and expediting, the focus of the effort should be on production using the four verbs: (1) design, (2) make, (3) transport, and (4) build.
It’s no longer about just ordering and waiting. You must now view the supply chain as a series of connected steps, from design to delivery. Each link in the construction supply chain has its own systems in place.
The challenge comes when the systems don't integrate or interact effectively, resulting in lost communications, confusion, and delays. Embracing the production mindset can turn supply chains into value streams that can be optimized.
#4 Plan and hold regular procurement meetings.
At a tactical level, regularly gather your team to align on procurement and supply chain management.
The purpose of the planning and procurement meeting is to enact long-term strategic planning where managers update their master schedule, prepare make-ready schedules from pull plans, and confirm they have the procurement tracking to the right dates.
Do a field walk.
Look at the model.
Call certain contractors.
Flip through the drawings.
Value-stream map the supply chain.
Consistent communication keeps the entire team proactive and in sync.
#5 Categorize your materials.
Not all materials are created equal. Different materials carry different risks, and therefore should be treated differently.
To understand how demand and behavior of your project’s production system might vary, start classifying your material supply flows into three categories:
Made to stock—Suppliers produce based on forecasted market demand for multiple customers.
Made to order—Suppliers produce standard products upon receipt of an order by specific customers.
Engineered to order—Suppliers produce unique products for a single customer upon completion of engineering (in some cases, suppliers develop detailed engineering for fabrication).
This additional layer of insight can help you tailor your strategy and minimize issues.
#6 Minimize lead times.
I’ve heard some crazy lead times. But no body asks why the lead times are so long and what can be done about it.
Build a habit to challenge and understand the elements of long lead times instead of accepting them as given. Look for ways to reduce these times by analyzing and optimizing each step in the supply chain.
Lead time: the duration from when an order is placed until the customer receives it.
Cycle time: the total time needed to complete the production of an item.
Raw process time: the actual time spent actively working on the item.
When lead times are excessive or out of proportion to cycle time, it’s usually an indication that operations can be improved. The best supply chain management plans involve shortening the chain wherever possible.
#7 Implement last responsible moment scheduling.
Last Responsible Moment (LRM) is a lean strategy of not making a premature decision but instead delaying commitment and keeping important and irreversible decisions open until the cost of not making a decision becomes greater than the cost of making a decision.
Start timing your material orders as close to their installation time as possible without risking delays. LRM reduces the need for storage and minimizes the risk of damage, loss, and delays on your project.
#8 Deliver today what will be installed tomorrow.
Whenever possible, arrange for materials to be delivered exactly when they're needed for installation—ideally, the day before. Your team will enjoy the benefits of:
Worker safety
Flow efficiency
Site cleanliness
Overall productivity
Operational stability
Timing is everything. Using materials right after they arrive is the hallmark of efficient procurement.
#9 Get everybody on the same page.
As much as possible, get everyone on a single system or platform. Shared communications portals allow all communications to stay in one place and visible to each company in the chain.
Along each step, everyone can see and track materials with ease, estimate arrival times, and make changes easily, streamlining the process for the shortest possible arrival times.
Shared technology platforms, like ConstructivIQ, increase collaboration and streamlines the entire end-to-end processes.
#10 Manage changes smartly.
Change is inevitable in construction. So expect and plan for changes in schedules, lead times, and requirements.
Review changes as they happen and understand the impact of these changes on procurement and in turn on the project schedule.
When you’re armed with data, you can stay flexible enough to mitigate impacts on your procurement plan.
Final Thoughts
Better supply chain management is about better planning.
If materials needed to execute work are not available, labor costs increase, and schedules can be delayed.
If too much material is on-site, cash is squandered or needlessly tied up while construction schedules may also be extended, to the detriment of the project.
In both cases, unnecessary risk occurs, while quality may be jeopardized.
Lesson: Get the right material to the site at the right time.
Once you understand these strategies, using the right tools begins to make all the difference. It means less time on administration and more time on strategy.
Ready to take your procurement efforts to the next level?
ConstructivIQ is on a mission to target these critical pain points in the construction industry by connecting people and data across silos. And the procurement challenge is their initial focus.
Book a demo and prepare to be amazed.
Until next week,
Kyle Nitchen
LAST WORD 👋
PODCAST
7 Archetypes of Effective Project Managers
I recently had the opportunity to talk about Project Management on the Contractor Evolution podcast! We talked about:
Why most projects typically fail.
How many modern tools + methods aren't cutting it in today's construction environment.
How to be an effective Project Manager.
Shout out to the Breakthrough Academy for bringing me on, it was great sitting down with you guys and sharing what's possible for contractors and project leaders today. This was a super fun one and I hope you enjoy it.
Listen to the episode here » Apple | Spotify | YouTube
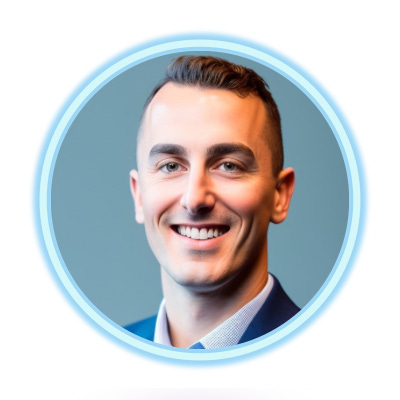
When you're ready, here’s how I can help:
Upgrade your PM software. Project financials, management, and construction admin. Switch to INGENIOUS.BUILD to evolve from an administrative project manager to strategic project leader.
Get my full toolbox (free). It contains 30+ software and hardware tools I’m using today.
Hold your schedule accountable. Gain stability and flow in your projects with this Takt Planning & Control online course. Use code “Influentialpmtakt” for 30% off!
Advertise in this newsletter. Put your brand in front of 2,500+ construction project managers, leaders, and execs. (Booked out 5 weeks)
Support this Newsletter. The Influential Project Manager articles will remain free, but if you find this work valuable, I encourage you to become a paid subscriber. As a paid subscriber, you’ll help support this work.