Why is it So Hard (and Expensive) to Build Anything?
The Hidden Dynamics of Construction Delays.
👋 Hey, Kyle here! Welcome to The Influential Project Manager, a weekly newsletter covering the essentials of successful project leadership.
Today’s Overview:
The construction industry has long been challenged by delays and inefficiencies, impacting both cost and productivity.
Even with advancements, traditional project management approaches haven’t solved these problems, leading to consistent issues in delivering projects on time and within budget.
What does it take to end the deep-rooted cycle of endless delays and overruns in construction projects?
By examining the evolution of construction management across three eras — Productivity, Predictability, and Profitability — we find ways to improve project management with a focus on combining production systems and adopting performance-driven strategies.
🏗️ Today’s Newsletter is Proudly Presented by Buildots!
Buildots, an award-winning leader in construction technology, introduces a performance-driven approach to project management by harnessing AI and computer vision. Using off-the-shelf wearable 360-degree cameras, our platform allows general contractors to seamlessly capture every detail of the construction process, comparing this data with the project's design models (BIM) and schedules.
Our solution automates progress tracking, delivering timely, unbiased data and actionable metrics, essential for performance-oriented decision-making. This enhances visibility and control for both site teams and management, ensuring projects progress efficiently and effectively. With Buildots, delays are minimized, collaboration is streamlined, and construction projects are completed on time and within budget, setting new standards in performance and productivity.
🔨 Why is it So Hard (and Expensive) to Build Anything?
Filed under: Construction, Project Management
Imagine it’s 2014, and I'm stepping onto a lively construction site in sunny Miami Beach, Florida.
Fresh out of college, eager yet inexperienced, I'm starting my first major construction project.
Before this, I had a mix of internships and jobs doing hands-on labor — the real gritty stuff.
On site, I quickly notice some of the industry's inefficiencies. Something felt off. We're juggling important RFIs and submittals through endless email chains, relying on sketchbooks for plans, and always tackling emergencies to keep our risk in check.
It's chaotic, disjointed, and everyone's in their own little world. This struck me as unproductive, yet it was the norm. I couldn’t help thinking, "Is this really how we do things?"
I was on a talented team, and we managed our project with integrity, striving to provide the best service possible. But despite our efforts, we found ourselves working harder rather than smarter due to the limitations that felt beyond our control.
As the new guy, I kept asking myself, "Why's this so tough? So inefficient?" Despite my reservations, I knew I needed to support my team. So, I adapted and became good at navigating these challenges. Over time, I'm nailing it, but the projects still felt like roller coasters – thrilling but not always smooth.
Fast forward to my light bulb moment: I read "Built to Fail" by Todd Zabelle. It was as if he was speaking directly to me, highlighting the deep-seated issues in project management that lead to delays and budget overruns.
This week, we’ll explore the evolution of construction through three key eras outlined by Todd, and how they've influenced our current project management challenges. It’s a fantastic breakdown of how our traditional project management methods came to be.
We'll discover how focusing on profitability, performance, production, and better use of your data can revolutionize project management. Let’s begin.
The Industry is Standing Still
The list of project cost and schedule runs seems almost infinite. Let’s look at some revealing statistics about our industry’s current performance.
According to 2017 McKinsey Global Institute report (McKinsey):
13% of the world’s GDP is contributed by the construction sector
5x higher productivity growth in manufacturing vs. construction over a 20-year period
$1.6 trillion USD could be added with a boost in construction productivity
85% of construction projects face cost overruns, often going up to 80% beyond budget in large projects.
According to a 2023 Labor Productivity Study (FMI):
$30 billion to $40 billion lost annually due to poor productivity
3 of the top 4 factors affecting productivity are related to (1) planning, (2) communication, and (3) collaboration.
79% of contractors could improve labor productivity by 6% or more with better management
50% average increase in profitability from a 6% productivity improvement
45% saw declining labor productivity
A series of independent studies revealed a direct link between poor contractor performance and inefficiency (Vertex):
18% coming from external factors
30% coming from clients
52% of delays are due to contractor issues, more than both owner and external factors.
62% of those are from management and supervision challenges
These figures underscore Todd Zabelle’s thesis:
“During the past century, we have created an approach to delivering capital projects that is built to fail. The more we implement elements of the current approach, the worse project outcomes become. Only through resolving this “gap” will we be able to solve the project performance challenge.”
This is not just a pattern; it’s ingrained in the industry’s DNA, leading to constant delays and budget overruns.
What underlying issues are we missing?
If we’re going to shape the future of project delivery, we need to understand how we got here. Broadly, we can separate the field of project delivery into three eras:
Era 1: The Era of Productivity (1900-1950)
Era 2: The Era of Predictability (1950 - Current)
Era 3: The Era of Profitability (2000 - Current)
For those involved in engineering and construction, especially senior-level professionals who understand these issues and are seeking solutions, keep reading.
The frequent problems of budget overruns, schedule delays, and overall project chaos are avoidable. There's a more efficient approach waiting to be embraced.
Era 1: The Era of Productivity (1900-1950)
“How do we get more out of workers?”
Era 1 was the first major era in construction management: The Era of Productivity, spanning from 1900 to 1950. This was a time of big changes and new ideas, but not all of them worked out so well for construction.
It was defined by the rise of centralized planning and a divide between planning and execution, which is where the inefficiencies began.
Key Thinkers of Era 1:
Frederick Taylor: Known as the pioneer of scientific management, Taylor separated the planning from the doing. He aimed to boost industrial efficiency by breaking down every task and optimizing it. This is called “resource efficiency.”
Henry Gantt: Known for developing the infamous Gantt chart. He contributed to project management by creating visual planning tools that help track project progress and align tasks. This tool is still used today, but it has its limits.
Frank & Lillian Gilbreth: This duo brought psychology into the workplace. They looked at what motivates workers and how their actions and needs can make work more efficient.
Daniel Hauer: He tried to bring Taylor's ideas into construction. This move started a gap between planning and actually doing the work on the ground, which wasn't ideal for the industry.
The focus was more on getting hard work done by craftspeople and calling it productivity. But in construction, this approach created issues on site.
In manufacturing, the process takes precedence, and that's why it kept getting better. In construction, though, ignoring the process didn't quite fit, leading to lower efficiency compared to other industries like auto manufacturing. We paid too much attention to using resources efficiently and not enough on making the work flow smoothly, which hurt the overall system.
The Rise of Bureaucracy
The era's bureaucracy further complicated matters. Thanks to Era 1, what was once simple became complex. Planners and schedulers, often detached from the actual work, relied on disconnected plans using tools like Gantt charts. These tools looked good on paper but didn't always translate well to real-life project needs.
This bureaucracy prioritized administrative tasks like accounting, reporting, compliance, HR, and risk management over actual construction activities like designing and making things. This approach set the stage for Era 2's obsession with predictability, further compounding administrative burdens.
In summary, the Era of Productivity was a time of trying new things, but it also showed us that what works in one industry doesn't always work in another, especially in construction.
Era 2: The Era of Predictability (1950 - Current)
“How do we get more predictable outcomes through measurement, compliance, & controls?”
Now let’s discuss Era 2 in construction management, known as The Era of Predictability. It's the time we're in now, and it's all about making project management more predictable.
Key Developments:
This era saw new project management methodologies such as the birth of CPM (Critical Path Method) and other methods like PERT (Program Evaluation and Review Technique), EVM (Earned Value Management), and AWP (Advanced Work Packaging). These are fancy terms for different ways to manage projects, recognized by the PMBOK (Project Management Body of Knowledge).
The focus was on managing time, cost, quality, risk, and procurement. Sounds good, right? But here's the catch – while these are important focusing too much on these aspects can make us overlook what really moves a project forward. Looking back, it’s clear we were missing a big piece of the puzzle.
The Critical Path Method
Introduced in 1959 by James Kelley and Morgan Walker, CPM was all about:
Planning and Predicting: Figuring out how long a project might take and planning it out.
Evaluating Options: Looking at different ways to reach the project's goals.
Tracking Progress: Keeping an eye on how the project's going compared to the plan.
Making Decisions: Using data to make smart choices in the project.
They talked about balancing time, cost, and quality – the almighty iron triangle.
But this framework didn't quite get everything right. It overlooked the important elements of Operations Science:
The study of the transformation of resources to create and distribute goods and services.
Era 2 also brought an overemphasis on administration functions – things like scheduling, reports, HR, and risk management. This focus led to more paperwork (lagging measures) and less time on actual performance based construction (leading measures). The industry got fragmented, and communication between everyone from owners to workers got harder.
The Rise of Construction Management
To address the risk created by Eras 1 and 2, general contractors turned into construction management firms. This meant general contractors became more administrators than producers, which compounded the disconnect. This shift even reached universities, where construction education started to push more on administration than production.
We got so caught up in planning and managing that we forgot about the real work – the building part. This approach led to what we see and experience now, consistent issues of delayed projects and budget overruns.
But now, we're on the brink of something new, what Mr. Zabelle calls Era 3. This is our chance to mix things up and make construction more integrated and efficient. We've started this journey, but there's still a long way to go. The challenge is to move past the limitations of the first two eras and embrace a more holistic approach in Era 3.
Era 3: The Era of Profitability (2000 - Current)
“How do we deliver a project using less cash and within optimal time?”
We’re now in the middle of the latest shift in construction management: The Era of Profitability. We're moving from paperwork to actual work – a change that began in the 2000’s. Now, it's all about designing, making, and building things.
We're looking at projects as a blend of different production systems. Think of operations science (OS) as our new best friend, helping us understand and manage these systems. Here, we’re unlocking additional value through introducing and managing new factors that were previously unconsidered:
Work in Process (“WIP”)
Process Design
Variability
Inventory
Capacity & Throughput
In the past, schedules (like Gantt charts or CPM schedules) told us what we hoped would happen. But what really drives a project? It's the production system. This includes everything from pouring concrete to steel fabrication. We're asking, "What's actually happening in each system, what’s the process, and how do they work together?"
Schedule vs. Production System
Here's a big change. We're differentiating between the schedule (what we plan to do) and the production system (how we're actually doing it). Traditional project management often missed this, focusing more on paperwork and what happened in the past.
Our challenge is to get a grip on the entire project production system. This means diving into each part – like concrete work, site grading, steelwork – and figuring out where the bottleneck is. Instead of just looking at schedules and budgets, we're zeroing in on how things are really getting done.
Era 3 is about changing our focus. It's not just about what we're delivering; it's about how we're doing it. This shift is all about putting on a new set of lenses and leveraging different data to become more proactive and efficient in managing our projects.
The Future of Construction Management with PDCM
What does it take to end the cycle of endless delays and overruns in construction projects?
The solution is Performance-Driven Construction Management (“PDCM”), a groundbreaking strategy developed by Buildots and top construction firms. The winning strategy is about shifting the focus to proactive metrics that forecast and shield against project pitfalls rather than simply documenting them.
The Core of PDCM: Measure → Analyze → Optimize
These three actions are your key to unlocking Era 3 in construction management. By focusing on these tasks, we shift from traditional administrative tasks to the core of project delivery – the actual construction work. In lean terms, this shifts the focus from non-value-added to value-added activities.
The Role of Accurate Data
For PDCM to work, accurate project data is required. You need a data system to help you measure, analyze, and optimize every aspect of your project. This system gives you real-time information, and turns it into actionable performance indicators that you can act on and make based decisions. It also helps you grasp the impact of any changes on time and cost, not just on one part of the project, but on the big picture.
Having this data at your fingertips means you can quickly adapt to change without wasting time gathering all the numbers before making a decision. So even though you can't avoid change, having a data system means you don't need to let it slow you down.
How Digital Tools Power PDCM
Collecting data the old way, by hand, isn't reliable—it often leads to more issues. To fill this need for accurate data collection, you need the right digital tool. That's where tools like Buildots step in. They use wearable 360-degree cameras and AI to gather data accurately and quickly, giving you a clear picture of your project.
These advanced tools not only collect the data but also process it automatically to provide a full progress report once or twice a week. In other words, it doesn't only see everything, it understands it. This means you can make better decisions, keep everyone on the same page, and move your project forward without delays.
Why Download the PDCM Whitepaper?
The time for business as usual is rapidly closing. The pain of the traditional management methods is going to increase exponentially as our capacity to execute projects fail to meet expectations.
We need to free ourselves from the prior eras and instead focus on the new era of project delivery, one in which projects will be highly efficient production systems that utilize the modern technology (AI, data analytics, etc.) we are privileged to have access to.
This Buildots whitepaper shows us new metrics designed predict and prevent rather than react and repair. Dive into the full framework and use it as your guide to better project outcomes. Here's what you'll discover:
Behind-the-Scenes Insights: Uncover the real reasons behind project delays.
Cutting-Edge Strategies: Learn new ways to manage projects.
Success Stories: See how others have turned challenges into victories.
Don't become just another statistic. Move beyond the outdated methods of Eras 1 and 2, and lead the charge into Era 3. Achieve your goals on schedule, every time.
For more insights into Performance-Driven Construction Management, read the full whitepaper.
Until next week,
Kyle Nitchen
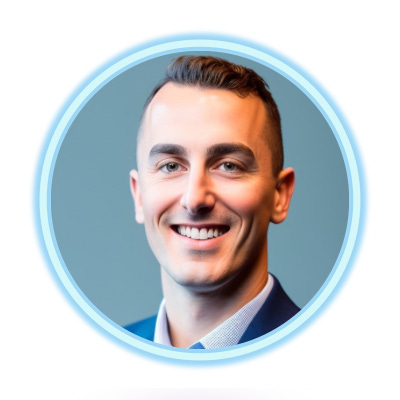
Whenever you're ready, there are 5 ways I can help you:
Get my first book! No Bullsh*t Project: A Project Manager’s Guide to Successful Project Leadership
Upgrade your scheduling software. Experience the future planning system for construction and real estate development. iPM subscribers get a 15% discount on the first year license.
Get my full toolbox (free). Access 30+ software and hardware tools I'm using today.
Learn Takt Planning. Elevate your skills as a scheduler, planner, and lean builder with the Takt Planning & Control online course. Use code "Influentialpmtakt" for 30% off.
Advertise in my newsletter. Put your brand in front of 6,000+ construction project managers, leaders, and execs. (Booked out 8 weeks)
Very interesting and well written article! I’m interested to learn if the PDCM model would work in other production type industries outside of construction.
Love the historical context. And I think these concepts hold true to planning in general—not just construction.