Mastering Construction Supply Chain
How to get the right information and materials at the right time.
👋 Hey, Kyle here! Welcome to The Influential Project Manager, a weekly newsletter covering the essentials of successful project leadership.
Today’s Overview:
80% of construction projects are delayed. These delays cost billions, frustrate stakeholders, and have plagued the industry for decades.
Procurement is at the heart of the problem, causing 40–50% of these delays. Why? Most systems can’t handle the level of detail required to get the job done right.
It all comes down to one goal: ensuring the right materials, in the right quantity, arrive at the right place, at the right time. This article breaks down practical steps and tools to help you overcome procurement challenges, and keep your projects on track.
Today’s issue is proudly presented by ConstructivIQ!
Minimize schedule delays by getting the right material to the project site at the right time.
Procurement planning is broken. Excel spreadsheets and siloed systems can’t handle today’s challenges. ConstructivIQ connects the entire procurement lifecycle to your schedule, driving collaboration, reducing risks, and cutting costs for everyone involved.
Project Engineers: Save hours tracking procurement effectively.
General Contractors: Lower project costs and apply lessons to future jobs.
Owners: Reduce schedule risk and make timely decisions.
Design Teams: Prioritize design sequences efficiently.
Learn more at ConstructivIQ.com and start improving your procurement process today.
🕒 Mastering Construction Supply Chain
Filed under: Project Management, Lean Tools & Tactics
The success of any construction project hinges not only on the visible, on-site work but also on the invisible workflows driving it—especially the supply chain.
The construction supply chain refers to the steps involved in getting tools, building materials, and other necessities to the jobsite.
When procurement and information flow are well-managed, projects stay on track and avoid costly delays. Unfortunately, this is where many project teams struggle.
To help you navigate the complexities, here are 5 proven strategies to master the construction supply chain:
1. Focus on the Invisible Workflows
Picture a construction site in full swing.
Concrete trucks rolling in. Cranes are lifting materials. Crews are framing walls and installing systems. This is the visible progress everyone notices.
But what powers this progress?
Behind the scenes, there’s a hidden workflow driving everything. Before anyone can build anything, there's a mountain of paperwork that needs to happen:
RFI’s
Permits
Contracts
Shop Drawings
Purchase orders
Design approvals
Staging, loading, & transporting
This is the workflow that’s hard to see and rarely prioritized.
If even one of these steps is delayed or incomplete, the entire project can grind to a halt—no matter how ready your crew is or how hard they work. Every activity in your schedule depends on a well-timed supply chain.
A project’s success isn’t just about pushing workers harder to meet schedule. It’s about ensuring the right information and materials are available at the right time.
2. Address Procurement Planning Gaps
Effective procurement is critical to completing a project on time and on budget. Yet, many project teams struggle because they rely on outdated, static procurement practices that fail to keep up with real-world demands.
Traditional procurement planning operates in silos. Teams are relying on:
Disconnected tools: Excel sheets that don’t sync with project schedules.
Rigid plans: Static roadmaps that don’t adapt to changing conditions.
Limited visibility: Stakeholders operating without a clear, unified view.
These gaps contribute to 40-50% of the delays and these rates haven’t changed over the last 10-20 years. A single delay—whether in materials, approvals, or delivery—can ripple across a project, throwing schedules into chaos.
The future involves treating your procurement plan as a dynamic, living document:
Tie it directly to your project schedule to keep everything aligned.
Build in buffer to adjust for changes and unforeseen delays.
Make hidden workflows visible by integrating procurement details into your planning tools.
By syncing it with your project schedule, you can bridge the gap between what’s planned and what’s actually happening.
3. Improve Information Flow
“Your projects don’t rise to the level of its goals. They fall to the level of your systems.”
Managing procurement extends beyond materials - you need to be procuring the contracts, training, tools, equipment, and information that accompanies your material.
Your system must allow for information to flow clearly and timely:
Distributed RFIs
Submittal packages
Change order approvals
Complete shop drawings
Installation instructions/training
Without this information flow under control, you’ll run into bottlenecks everywhere.
Invest in a supply chain production system that integrates procurement with your production plan. This ensures teams have everything they need—materials, tools, and information—at the right time.
4. Centralize Your Processes
Fragmented supply chain management leads to delays, miscommunication, and risk.
Tim Jed, DPR Construction’s supply chain lead, describes how centralization transformed their operations:
“We procure things on a project-by-project basis, and materials are generally bought through subcontractors, so the general contractor doesn’t always have a line of sight to what’s going on with the material supply chain. Centralizing our processes allowed us to proactively address issues instead of reacting too late.”
Source: Construction Dive
Most contractors are still using splintered systems and manual spreadsheets, because it’s not easy to build a tech stack that supports centralized access to critical supply chain metrics.
By bringing your processes together, you’ll reduce delays and immediately gain better control of your supply chain.
5. Adopt the Right Tools
I love solving the challenges that come with scheduling, planning, and procurement.
Over the years, I’ve relied on a few digital tools that streamline my workflow and keep projects on track. Here are my top recommendations:
🔨 Tool #1: Outbuild
Simplify Last Planner System® Implementation.
What is does:
Outbuild is an easy-to-use scheduling and planning tool that integrates with the Last Planner System®.
How it helps:
Tracks roadblocks and constraints.
Generates lookaheads directly from your master schedule.
Provides real-time updates and the data you need to continuously improve.
Why I trust it:
It’s intuitive, easy, and saves my team hours of planning time. The reporting features—like Percent Planned Complete (PPC), Reason for Variance, and S-Curve analysis—deliver actionable insights for continuous improvement.
🔧 Tool #2: Miro:
Collaborate and Visualize Projects.
What it does:
Miro offers digital whiteboards, perfect for mapping out processes, brainstorming, and aligning teams.
How it helps:
Create of pull plans, Scrum boards, process maps, A3 reports, flowcharts, and more.
Visualize ideas and turn them into actionable plans.
Simplify team collaboration, even across remote locations.
Why I trust it:
Miro makes complex ideas clear and collaborative. Whether I’m aligning teams or creating workflows, it’s my go-to for effective communication and planning.
🛠️ Tool #3: ConstructivIQ
Streamline Material Procurement.
What it does:
ConstructivIQ integrates the procurement lifecycle with your schedule for real-time visibility and tracking.
How it helps:
Tracks material progress with visual indicators.
Breaks down procurement by zone, area, or work package.
Identifies delays and generates “Make Work Ready” reports.
Tracks schedule changes to understand procurement impact.
Why I trust it:
On a six-phase surgery renovation project, ConstructivIQ helped me flush out all the procurement bottlenecks in record time. It replaces outdated spreadsheets, mitigates risks, and ensures materials arrive exactly when needed. It’s the solution the industry has needed for years.
If you end up using these tools, let me know what you think!
They’ve made a huge difference in my projects, and I’m always curious to hear how others put them to work.
Until next week,
Kyle Nitchen
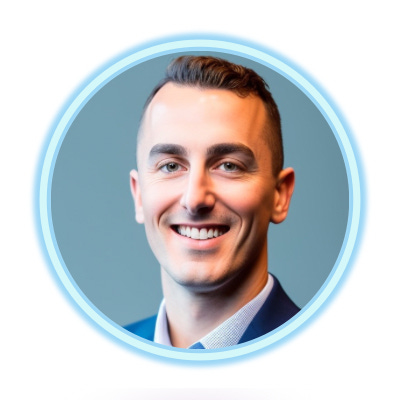
Whenever you're ready, there are 5 ways I can help you:
Get my first book! No Bullsh*t Project: A Project Manager’s Guide to Successful Project Leadership
Upgrade your PM software. Experience the future operating system for construction and real estate development.
Get my full toolbox (free). Access 30+ software and hardware tools I'm using today.
Learn Takt Planning. Elevate your skills as a scheduler, planner, and lean builder with the Takt Planning & Control online course. Use code "Influentialpmtakt" for 30% off.
Advertise in my newsletter. Put your brand in front of 4,750+ construction project managers, leaders, and execs. (Booked out 5 weeks)