How I Would Build a Data Center in 2025
The blueprint for tackling AI-ready infrastructure projects.
👋 Hey, Kyle here! Welcome to The Influential Project Manager, a weekly newsletter covering the essentials of successful project leadership.
Today’s Overview:
The future of the digital world depends on the quality of today’s data centers.
The rise of artificial intelligence is fueling exponential demand for computing power, and major players like Microsoft, Meta, Google, and the United States are pouring billions into specialized AI facilities.
If I were to manage a data center project today, and wanted to deliver it without chaos, here's exactly how I'd approach it.
🚚 Today’s issue is shipped to you by Krane!
Is managing your delivery schedule a never ending game of telephone?
When schedules are scattered across emails, texts, and individual planners, things fall apart fast. Missed shipments. Miscommunication. Downtime on site. It’s a problem we know all too well, and it’s costing teams valuable time and money.
It doesn’t have to be that way! With Krane’s Free Delivery Board, you can book, manage, and track deliveries all in one place. Visit Krane.com to get started today and experience seamless delivery management firsthand.
🤖 How I Would Build a Data Center in 2025
Filed under: Construction, Project Management
What if I told you that the future of the digital world rests on how well we build today’s data centers?
We're witnessing the largest and fastest infrastructure boom in history, driven by an unprecedented surge in artificial intelligence (AI). Companies like Microsoft, Meta, and Google are investing billions into specialized AI facilities, making the stakes for successful data center delivery higher than ever.
These aren't your typical server farms. AI computing requires specialized cooling systems, immense power densities, and highly complex infrastructure integration. A single day of delay can cost millions in lost revenue. The margin for error? Zero.
Consider the scale:
Microsoft is investing $80 billion in AI-specific data centers.
Google plans to spend $25 billion on expanding its AI infrastructure.
The U.S. has announced a $500 billion AI infrastructure investment.
Like many project leaders watching this boom, I've been thinking deeply about what it takes to deliver these highly complex projects successfully.
While I haven't built a data center before, I've managed equally complex projects including beachfront hotels and healthcare facilities - where precision, speed, and flawless integration were critical.
If I were to manage a data center project today, and wanted to deliver it without chaos, here's exactly how I'd approach it.
Build the right team.
Create a rock-solid plan.
Manage the supply chain like a pro.
Shape a culture that delivers.
Commit to continuous improvement.
In this newsletter, I’ll unpack the philosophies, principles, methods, and tools behind these five components—drawing from industry leaders and proven frameworks. Whether you’re managing a data center, a hospital, or any high-stakes project, these ideas will help you deliver with confidence.
Let’s dive in.
Special thanks to these incredible resources for shaping this framework:
The First Planner System (Jason Schroeder, Elevate Construction)
How Big Things Get Done by Bent Flyvbjerg & Dan Gardner
Built to Fail by Todd Zabelle
Step 1: Building the Right Team
🧠 Philosophy: Great projects are built by great people.
No amount of spreadsheets, planning, or technology can compensate for a poorly built team. In my experience, the team’s quality determines 90% of a project’s success. Complex facilities with tight deadlines demand more than technical skill—they require collaboration, trust, and alignment at every level.
We want to get the right people on the bus and the wrong ones off. After that, the core philosophy centers on maintaining team health and capacity throughout the project lifecycle - technical excellence flows from well-supported, high-performing teams.
🗝️ Team Building Principles:
Trust: Build psychological safety by leveraging individual strengths and establishing clear roles. Trust empowers people to perform at their best.
Conflict Resolution: Address challenges early with structured, collaborative problem-solving before they escalate into bigger issues.
Commitment: Build engagement by connecting each person’s role to clear project goals. People work harder when they understand their impact.
Accountability: Set and enforce high performance standards across all levels of the team. Accountability fuels results.
Performance Goals: Align the team around a shared vision—everyone climbing the same mountain together.
Leadership: A great leader leads by example. Discipline, consistency, and selflessness set the tone for the entire team.
♻️ Methods for Success:
Right people, Right roles: Matching skills to roles creates a well-oiled machine. I’d begin by selecting the team, identifying leaders, and conducting a DISC assessment. This tool reveals strengths, stress points, and behavior patterns, ensuring each person is placed where they’ll thrive.
Leader standard work: Consistency is key. I’d establish daily and weekly routines to support the team, including site walks, schedule reviews, one-on-one check-ins, and mentoring future leaders. Great projects create great builders.
Capacity Planning: Burnout kills productivity. I’d carefully monitor workloads, track hours and stress levels, and redistribute tasks or bring in resources as needed. A fresh, energized team makes better decisions and delivers superior work.
Clear Communication: Effective communication isn’t about what you say—it’s about what others understand. Every email, meeting, and report would follow clear communication protocols to ensure alignment. Miscommunication is a silent project killer.
Team Alignment: Weekly alignment sessions keep everyone on track. Using a structured format (status review, issue identification, solution development, and action items), these meetings ensure priorities are clear and commitments are met.
🛠️ Tools:
Microsoft Teams: Enables digital SCRUM boards and real-time collaboration across project stakeholders.
Cogram: Streamlines meeting minutes, action item tracking, and reporting for improved team efficiency and meeting experience.
Miro: A digital whiteboard tool for visualizing workflows, sharing information, and enhancing team collaboration.
DISC Assessments: Data-driven insights for building strong teams and improving communication.
RACI Matrices: Ensures accountability and clarity in decision-making across functions.
Step 2: Create a Rock Solid Plan
🧠 Philosophy: Think Slow, Act Fast
A strong plan saves time, money, and headaches. Rushing into execution without detailed planning is one of the most common mistakes seen on construction projects. As Bent Flyvbjerg’s research proves, projects that over-index on optimism in planning almost always face delays and cost overruns.
Planning is cheap. Execution is expensive. Every hour spent designing and optimizing the production plan saves days of execution time and millions in potential delays. The key isn't the plan itself, but rather the systematic thinking that emerges from the planning process. By planning methodically, we create the conditions for rapid, efficient execution.
🗝️ Planning Principles:
“Plans are nothing. Planning is everything.” - Dwight D. Eisenhower
Start with the End in Mind: Understand commissioning and operational requirements from the start. Reverse-engineer the plan to meet those goals.
Optimize the Whole: Ask people to shift their focus from one that is chiefly concerned with individual work to one that is driven with the whole of the project in mind.
Risk Visibility: Maintain dynamic risk assessment processes that identify and mitigate issues before they impact production. Prevention beats reaction every time.
Phase Control: Break the project into manageable phases with clear handoffs and quality checkpoints. This keeps progress measurable and manageable.
Zone Control: Divide the project into distinct geographical areas, or "zones," to allow for focused management and monitoring of work flow within each area.
Buffer Strategy: Include time and resource buffers to protect critical path activities and maintain workflow. Buffers are your safety net, not wasted time.
Performance Visibility: Deploy real-time metrics that give teams immediate feedback on production performance. What gets measured gets managed.
♻️ Methods for Success:
The Last Planner System® + Takt Planning: The core of our approach centers on the Last Planner System, augmented with Takt planning to create a realistic timeline and an optimized production sequence. Weekly make-ready and work planning sessions bring together superintendents, foremen, and trade partners to identify and resolve bottlenecks before they become problems. Each week, we use data and analytics to refine the process and drive continuous improvement.
Commissioning Plan: All fire alarm, fire sprinkler, electrical and HVAC systems to be fully commissioned to finish the project. To succeed, these elements must be fully integrated into the production plan from day one. Failure to do so will result in delays and jeopardize the project timeline. While the process is complex, I know from experience the benefits of a thorough and well-executed commissioning plan are well worth the effort.
Change Management: No plan survives contact with reality, which is why a structured Change Management Process is critical. We would implement a structured process with clear communication and streamlined approvals to handle changes efficiently and prevent scope creep.
Risk Management: A Risk & Opportunity Log is a must. Updated weekly, this tool allows the team to identify, monitor, and mitigate risks while capitalizing on opportunities. Intellectual capital, not financial capital, should be the first line of defense in managing risks.
Quality Assurance: I’d adopt Jason Schroeder’s Trade Partner Preparation Process: (1) buyout alignment, (2) pre-mobilization planning, (3) pre-construction coordination, (4) first-in-place inspection, (5) follow-up verification, and (6) final validation. I love this systematic approach because it ensures every trade is ready for success when scheduled.
Budgeting: Let’s not forget to treat the project like a business. Weekly cost forecasting and report management keep expenses on track. Accurate forecasting prevents surprises.
Habits to Stay on Track:
Pull Planning: Plan every milestone at least three months ahead.
Pre-construction Meetings: Hold meetings three weeks before each trade mobilizes.
Lookahead Planning: Use six-week lookahead schedules to view upcoming activities and make the work ready.
Daily Routine: Spend 30 minutes reviewing drawings and schedules, followed by field walks to stay connected to the work.
🛠️ Tools:
INGENIOUS.BUILD: Serves as the central operating system for project financials, project management, and construction administration, with full tool integration.
Outbuild: Supports the Last Planner System® execution, with features for master scheduling, look ahead planning, make-ready planning, weekly work planning, and analytics.
Pixly: Centralizes photos, markups, and punch lists in one incredibly user friendly platform.
Siteaware: Provides AI-powered verification of installed work against design intent for proactive quality management.
Step 3: Supply Chain Management
🧠 Philosophy: From Just-in-Case to Just-in-Time
Traditional construction takes a relies heavily on buffering inventory - get everything on site early to avoid potential delays. This "just-in-case" mindset creates significant inefficiencies, tying up millions in capital while consuming valuable site space. Drawing from Todd Zabelle's project production management principles, we need to fundamentally rethink material flow in data center delivery.
Modern data centers demand sophisticated supply chain integration that synchronizes material delivery with installation sequences. This isn't just procurement - it's creating an orchestrated production system where every component arrives when needed, maintaining flow while minimizing work-in-process.
🗝️ Supply Chain Principles:
Control WIP: Work-in-process inventory is a proxy for time. Less WIP means faster completion.
Last Responsible Moment: Order and deliver materials based on actual installation needs rather than arbitrary milestones.
Focus on Flow: Align material deliveries with installation sequences to maintain continuous work flow.
Control Points: Identify critical points in the supply chain and monitor them rigorously.
Capacity Management: Balance resource utilization across the supply chain to prevent bottlenecks.
Strategic Buffering: Place inventory buffers at critical points to protect workflow, not just for convenience.
Information Flow: Integrate procurement of approvals, documentation, training, and support resources alongside physical materials.
♻️ Methods for Success:
My approach would center on project production management (PPM) principles pioneered by industry leaders. First, we'd map the entire value stream for critical components - from switchgear and generators to cooling systems and racks. This reveals opportunities to optimize lead times and reduce unnecessary inventory.
We'd implement supply flow control (SFC) using a constant work-in-process (CONWIP) protocol. This means maintaining strict control over how much material enters the system, preventing the buildup of excess inventory while ensuring critical resources are always available.
Our weekly procurement coordination meetings would focus on several items:
Review look ahead schedules.
Update procurement software.
Engage key suppliers and stakeholders.
Confirm procurement is on track to feed the system.
What roadblocks need to be removed or absorbed?
Are we on track with pre-construction meetings?
For specialized equipment like generators and UPS systems, we establish dedicated tracking processes with clear control points. Regular factory visits verify progress and quality, while digital tools provide real-time visibility into material status.
🛠️ Tools:
Krane: Digital supply chain platform that replaces static procurement logs for real-time material tracking and delivery management.
Krane Delivery Board: Digital delivery board that replaced static whiteboards to track shipments in real-time, align schedules, and ensure materials arrive on-site exactly when needed
Logistics Map: A plan to visually show the point of receipt for materials and labor, how materials and labor move through the site, staging locations, access points for bringing materials into the structure, and much more.
Project Safety Plan: A plan that details the entire site and defines: (1) access and egress points, (2) the emergency gathering point, locations of fire extinguishers, water, ice, emergency shut-offs, first aid stations, and more.
Step 4: Shape a Culture That Delivers
🧠 Philosophy: Respect for People
Project success flows directly from culture, which is reflected through daily experiences, actions, and behaviors. While metrics and reports are helpful, the true indicators of cultural health appear in clean jobsites, professional facilities, and engaged crews. This is especially crucial in high-stakes environments like data center construction, where aggressive schedules can tempt teams toward shortcuts.
Culture begins with leadership. The best project environments arise when leaders are consistently present, engage directly with crews, and set clear, visible standards. As the Executive Director from Sutter Health said at LCI Congress 2024, “You need to get the mindsets of the people working on the job in the right spot. So when there’s a long list of reasons why the project might be late, everyone’s response is to get in a room and fix it.”
If you want to change a project’s culture, change how people experience it, moment by moment.
🗝️ Culture Principles:
Respect for People: Every voice matters, and every contribution is valued.
Safety Leadership: Make safety a core value through constant focus and zero tolerance for shortcuts.
Open Communication: Create channels for feedback and recognize positive contributions publicly.
Time Efficiency: Treat everyone's time as the valuable, non-renewable resource it truly is.
Project Standards: Build pride through impeccable site conditions, clean facilities, organization, and purposeful setup.
Strong Onboarding: Create an incredible first impression with clear understanding and alignment.
Work Environment: Design conditions that motivate and energize the workforce.
♻️ Methods for Success:
Daily Morning Huddles: Daily huddles form the cornerstone of cultural reinforcement. These 15-minute gatherings save hours of potential confusion while building trust across trades. The focus is on listening to workers and supporting their needs, rather than issuing directives.
Invest In Facilities: Facility investment signals respect for the workforce. Providing superior restrooms, dedicated break areas, and thoughtful amenities shows respect for the workforce. These small investments pay off with improved productivity and retention.
The Eight Wastes Framework: Systematically eliminating waste would be top priority. This includes mindfully:
Eliminating unnecessary motion through optimal site layout
Preventing overproduction by matching work to demand
Minimizing inventory through just-in-time delivery
Reducing transportation with strategic material placement
Avoiding excess processing through clear work standards
Decreasing waiting time between activities
Managing defects through quality at the source
Leveraging workforce creativity and wisdom
🛠️ Tools:
Genda: Provides integrated platform for workforce management, site logistics, site communication, and safety coordination.
Visual Day Plan Board: A physical board that displays daily plans and performance metrics at the huddle location.
Recognition Programs: Structures celebration of wins and reinforcement of desired behaviors.
Step 5: Commit to Continuous Improvement
🧠 Philosophy: Small changes make a big difference.
It’s easy to overestimate the importance of one defining moment and underestimate the power of small, consistent improvements. My goal as a construction manager is simple: Build remarkable people, who build amazing teams, who build high-quality, profitable projects. Notice the order—people and teamwork come before the work or the money.
Leadership drives this process by investing in people, creating an environment where learning and innovation thrive, and ensuring every team member finishes stronger than they started.
🗝️ Principles:
Growth Mindset: We must see challenges as learning opportunities.
Leadership Pipeline: Develop tomorrow's leaders through mentoring and structured skill-building.
Lead by Example: Model integrity, discipline, and innovation.
Learning Culture: Encourage knowledge sharing and experimentation at all levels.
Knowledge Transfer: Capture lessons learned to benefit future projects.
Innovation Focus: Create safe spaces to test and implement new ideas.
♻️ Methods for Success:
Effective Onboarding: Craft meaningful orientations that clarify roles and connect individuals to the team and project vision.
Ongoing Training: Something I’ve done is host monthly workshops on technical and interpersonal skills, led by team members or industry experts, to encourage learning and growth.
Leadership Development: Identify high-potential team members and prepare them for leadership roles by teaching delegation, communication, and inspiration.
Feedback Loops: Conduct one-on-one check-ins, peer feedback sessions, and after-action reviews to identify areas for improvement and celebrate wins.
🛠️ Tools:
LinkedIn Learning: Offer access to diverse courses on leadership, communication, and technical skills.
A3 Problem Solving: Use structured methods to tackle challenges and drive improvements.
Plus/Delta: End meetings and milestones by asking two simple questions:
Plus: What produced value during the session?
Delta: What could we change to improve the process or outcome?
Final Thoughts
Writing this was both enjoyable and reflective, and I hope you found value in it. These ideas build on the work of great leaders in our industry, and I’m grateful for their inspiration.
While I haven’t built a data center before, the principles that have delivered successful healthcare projects—respect for people, thorough planning, supply chain excellence, strong culture, and continuous improvement—would be my starting point.
No plan survives contact with reality unchanged, but the balance between planning and flexibility, process and innovation, individual excellence and team performance is what defines great leadership.
As the demand for data centers accelerates, those who master these fundamentals and embrace adaptability will lead the way. The future belongs to teams that can think deeply, plan thoroughly, and execute with precision while remaining flexible.
What do you think about this approach? I’d love to hear your insights—what would you add or do differently? Let me know in the comments below.
Until next week,
Kyle Nitchen
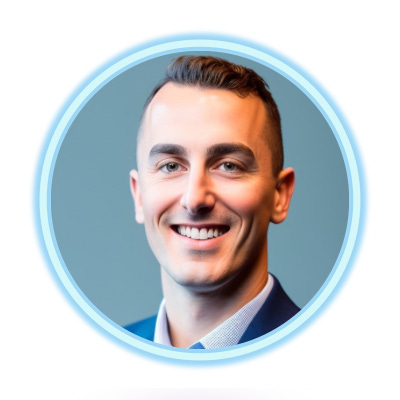
Whenever you're ready, there are 5 ways I can help you:
Get my first book! No Bullsh*t Project: A Project Manager’s Guide to Successful Project Leadership
Upgrade your scheduling software. Experience the future planning system for construction and real estate development. iPM subscribers can enjoy a 15% discount on first year license.
Get my full toolbox (free). Access 30+ software and hardware tools I'm using today.
Learn Takt Planning. Elevate your skills as a scheduler, planner, and lean builder with the Takt Planning & Control online course. Use code "Influentialpmtakt" for 30% off.
Advertise in my newsletter. Put your brand in front of 5,500+ construction project managers, leaders, and execs. (Booked out 5 weeks)